Applied Mobile Technologies and Interfacing with Robotics Software: Developing Improved Approaches for Cleanrooms
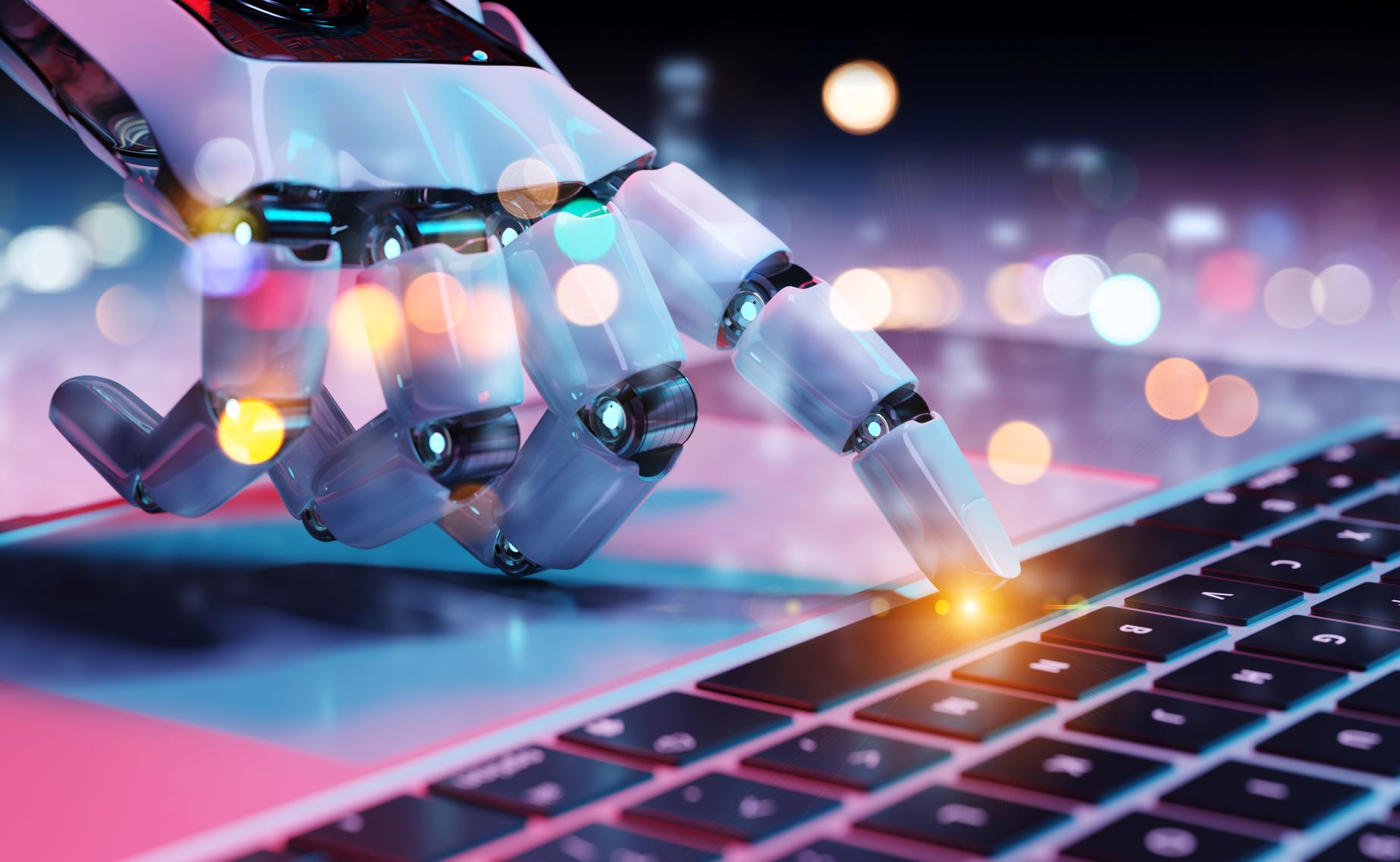
Applied mobile technologies in cleanrooms are a major focus of conversation for pharmaceutical developers. As the demand for upscalability increases, there is a pressing need for mobile robots which can fulfil the roles of their human counterparts without causing issues with contamination. However, there are several hurdles which have to be overcome before mobile robotics can be fully rolled out on the factory floor. Chief among the issues are procedures surrounding sterilisation, as well as ensuring that the robots have the capability to perform the tasks required of them.
At Pharmaceutical Mobile Robotics in April 2022, a panel led by Carl-Helmut Coulon, Head of Future Manufacturing Concepts at INVITE GmBH, discussed some of the major challenges surrounding the development and implementation of mobile robotics at this scale. Among the industry experts speaking with him was Faouzi Grebici, Industry Solutions Manager EMEA at Omron.
Some of the major discussion topics involved the panel’s expectations and visions for mobile robotics, their integration in present-day production environments and how they may be implemented in future environments. But what are the main considerations for integrating a mobile robot into a production environment?
Best Practice in Mobile Robotics Integration
At present, a key focus in industry is the integration of applied mobile technologies into a production environment. One panellist asserted that the introduction of mobile robotics solutions had to be tested prior to their implementation in production. “What we see at the moment in the industry is a lot of discussion of case studies around possibilities for using a mobile robot in an aseptic fill finish line,” he said. “There are a lot of use cases ongoing, but you can imagine you cannot simply install a robot in such an industrial environment.”
- Out Now: Oxford Global's R&D Key 40 Stories
- The Mobile Robotics Sprint: Developing a Mobile Robot for Cleanrooms
- Repurposing Space Robots for Remote Healthcare
In this context, a testing space for mobile robotics solutions in a mock-up would be a more desirable approach, with the option to transfer to production if successful. Integration costs can also be a significant hurdle for mobile robotics: for many, a key focus is on making the implementation of mobile robotics more affordable. Often the obstacle is that the robot itself is inexpensive, but when the integration costs are factored in they can be much greater. In this context, costs can only be driven down if the issue is approached by the industry as a collective to achieve a higher degree of standardisation.
Hurdles Associated with Non-Standard Automation
Another obstacle to the standardised implementation of mobile robots is the lack of a pre-existing mass-produced model. As Coulon surmised, “It’s not like they are sold in thousands with pre-standard applications. They are used for more flexible integration, or even asynchronous integration.” The needs and demands of any one manufacturer will vary from company to company, or even from factory to factory. Faouzi Grebici asserted that mobile robots should be considered as mobile machines and autonomous mobile robots (AMRs) are a ‘transportation brick’ within the total system. “Hence our role as robot provider is to ensure that this brick is ‘integration-ready’,” he explained; “Hence covering the mechanical, the control and the data-management integration aspect.”
Going back a decade, the cost of the technology for mobile robotics was decreasing, but the cost of engineering integration remained high. Implementing more concisely defined standards could provide a solution through enabling a large number of integrators to do the job and get the cost down. While digital and software solutions are available, some of the main hurdles are the hygienic design of mobile robotics.
Major considerations for this design included using the correct materials and the right microbiological aspects, as cleanability is another big focus in the design of mobile robots. A complication of applied mobile technologies in cleanrooms is that the strength of the cleaning solutions used to sterilise the robots is such that it can corrode the robot’s casing.
Global Production of Mobile Robotics in Cleanrooms
Discussing examples of other industries which have implemented an international standard approach to production, Coulon gave the example of superconductor manufacture. “The superconductor industry can more or less group their production lines together. I don’t see anything like this in any other industry, but for me this would be the premium solution for integrating mobile robotics.” Another panellist broadened the scope out to other areas of manufacture where mobile robots were being applied, adding that robots involved with the delivery of consumables and removal of waste would be cheaper because they did not have to comply with highly specific laboratory regulations.
While these applied mobile technologies would be cheaper, issues may arise regarding the systems used for integration of different operating systems. “As you move these robots into the production line, it’s more likely they’re taking their commands from an NES system rather than a LIMS (laboratory information management) system,” the panellist continued. They predicted that integration would become more complicated as laboratory and production lines began to merge, as with cell and gene therapy.
Future Goals in Integrating Applied Mobile Technologies
Various regulations concerning cleanroom design and hygiene specifications predicate the introduction and application of mobile robotics in the lab. Collaboration with the data validation of software for the implementation of good manufacturing practice (GMP) environments would be a help in this scenario. A big emphasis is on the need for data to be traced. Coulon made the case for an auto-trail approach intrinsically built into the automation system to record operational data in applied mobile technologies.
“We know exactly what is needed,” said Grebici. “All the data and information is in the robot. It is just a case of extracting it in a format that is acceptable.” If robotics information can be accessed in a manner which is pharma-compliant and aligns with the needs of the industry, it will be a massive boost to the implementation of mobile robots in pharmaceutical environments. “We as the applying industry get solutions not only from a mobile robot system capable of operating equipment, but also in the quality control area,” said Coulon. “This would definitely cut down costs towards the data integration aspect.”
Want to read more about the integration of mobile robotics into pharmaceutical production lines? Head over to our PharmaTec portal for up-to-date insights from the industry’s best and brightest. If you’d like to learn more about our upcoming Pharma Automation & Robotics UK: In-Person conference, visit our event website to download an agenda and register your interest.